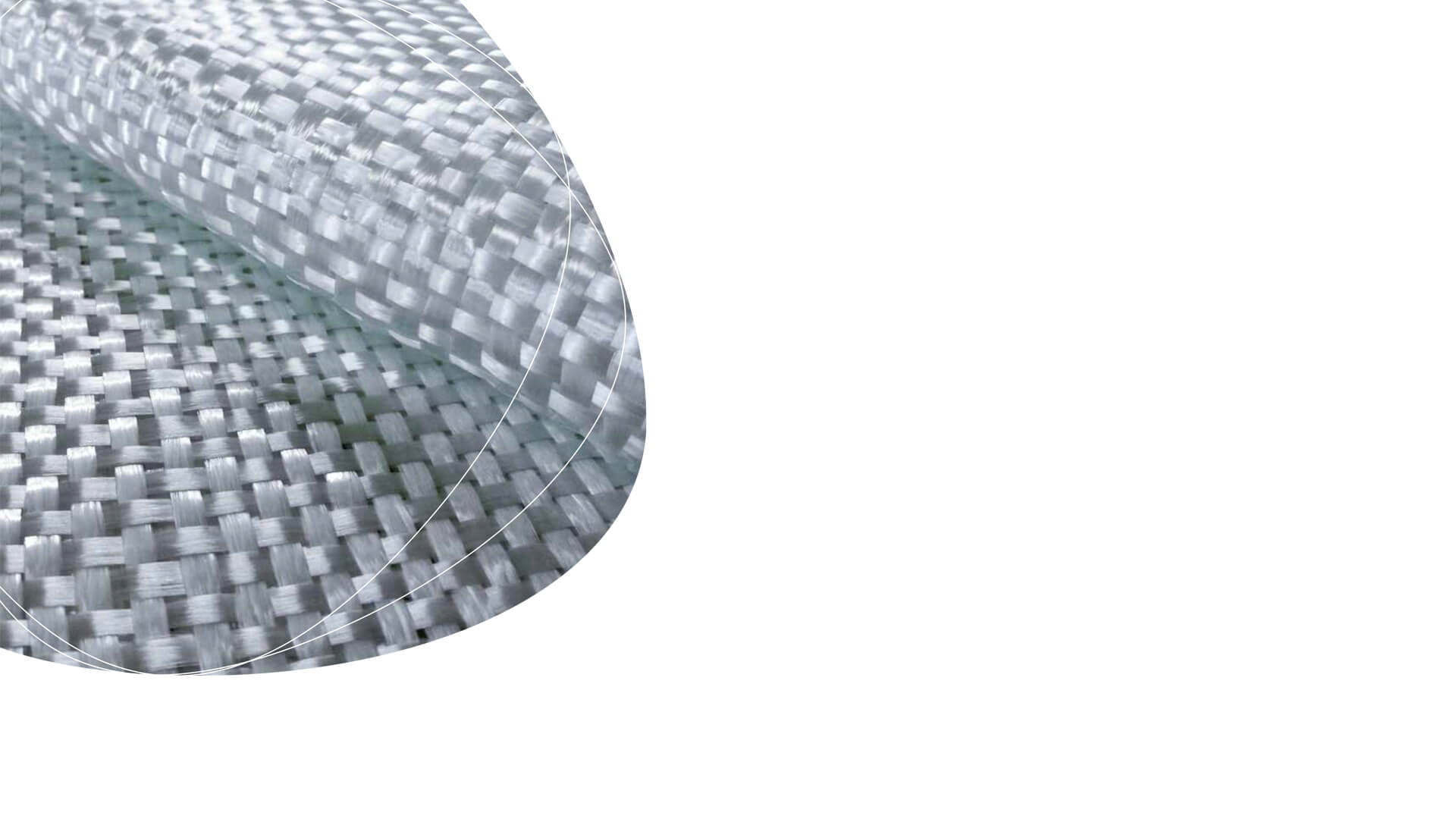
Our composites portfolio - top solutions for top performance thermosets
Our additive portfolio for thermosets contains products for a wide range of applications including advanced composites. Through this portfolio, we serve all technologies employed within the industry (for example sheet and bulk molding compounds, pultrusion, infusion hand lay-up/spray-up etc.).
Our products are suited to unsaturated polyester, vinyl esters, epoxy, polyurethanes, or acrylates. Applications include fiber-reinforced composites, gel coats and casting compounds, electrical and electronics insulations, polymer concrete, as well as engineered and artificial stone.
The wide range of customers we serve within these markets reflects the different stages of the value chain in the industry. Our customers include resin producers and formulators as well as producers of final components. They employ our additives to improve material qualities and properties, but also to ensure the efficiency of their production processes.
Given the fast market pace with constantly evolving trends and growing expectations regarding sustainability, our customers rely on us for innovative answers based on our long-standing expertise. Our most recent developments in this field are proof of that expertise; they include the world’s first coupling agent for carbon fibers (BYK C-8013).
To assist our customers who want to reduce their workplace hazards, we created a group of styrene emission suppressants for unsaturated polyester resins in particular. They comply with current health & safety regulations.
Our additive portfolio helps optimize different aspects of thermoset systems. Coupling agents, for example, contribute significantly to the mechanical strength of polymer concretes or fiber reinforced systems. Our rheology additives and air release agents improve the material’s processing qualities, whereas wetting and dispersing products affect its storage ability. Surface-active products improve the substrate wetting and the material’s leveling qualities. To ensure efficient and reliable manufacturing, our processing additives often combine a number of effects, such as mold release plus surface enhancing properties.
At BYK, we support our customers with services from our labs in order to test our additives in their applications, if needed. For example, we employ our sheet molding press to identify suitable products for fiber-reinforced compounds.
Our additives support a wide range of applications from many different industries. Customers benefit in many ways. Our processing aids help to establish highly reliable production processes, whereas our functional additives optimize the properties of the end product. The results are composites with flawless surfaces and extraordinary mechanical properties.
The automotive industry employs components based on thermosets for a multitude of applications, e.g. trims, trunk lids, or head-lamp housings. During sheet and bulk mold compounding (SMC/BMC), our products help to optimize production processes, making these processes highly reliable. Thanks to their excellent release properties after molding, our processing additives, e.g. BYK-P 9065, deliver immaculate component surfaces. Our wetting and dispersing products, notably BYK-W 9010, improve the resin’s flow behavior during production.
Materials used in structural components for the hulls of ships or yachts benefit in many ways from our additives. For an optimal flow behavior and processing, we recommend RHEOBYK-R 605 in these materials. To ensure the necessary nonporous properties of gelcoats for the boat’s outer skin, we recommend the use of our air release agents during production. BYK-A 555 has proven particularly successful in this context. Surface additives like BYK-330 improve the material’s substrate wetting. In open mold processes with hand lay-up or spray-up technologies, our styrene emission suppressants, e.g. BYK-S 750 N, reduce workplace hazards and optimize working conditions.
Our additives improve a variety of materials used in the construction business. They include polymer concrete for piping, artificial or engineered stone as well solid surface materials applied in interiors, e.g. kitchen benches. First and foremost, producers use our coupling agents, e.g. BYK-C 8000, to improve the material’s mechanical strength and its load-bearing capacity. Additionally, our wetting and dispersing products, e.g. BYK-W 908 and BYK-W 909, contribute to the resin’s optimal flow behavior during manufacturing.
Electro and electronic applications for our additives involve circuit boards, components, electrical insulation, and electrical casting. Here, the challenge is to ensure a perfect flow behavior of the resin during application. Moreover, flawless wetting properties as well as utmost air release are needed to achieve optimal results. To this end, we provide BYK-088 for air release, BYK-W 985 for wetting, and BYK-310 for substrate wetting.
Lightweight construction based on carbon fibers is in high demand within the transportation industry, since these advanced composites contribute to the production of energy efficient vehicles. Reliable manufacturing processes for these materials hinge on an immaculate wetting of the fibers to ensure the component’s mechanical strength. Moreover, perfect wetting is the only way to reduce rejects to a minimum, if not altogether.
Our innovative additive BYK-C 8013 is specifically designed for carbon fibers. Its unique chemical composition allows bonding of those fibers to the resin matrix. As a result, the finished parts are more resilient. In hot curing processes, e.g. sheet or bulk molding, pultrusion, prepeg or RTM, the component’s mechanical strength increases by up to 70 %. Besides, our processing aid BYK-P 9920 also adds to optimal fiber wetting.
Golf or tennis clubs, and fishing rods are mostly made of carbon fiber reinforced materials. To improve material properties, we recommend this specific wetting and dispersing additive: BYK-9076. It is particularly suited to the pultrusion production process.
We support the production of rotor blades for wind turbines in many ways. Our coupling agent BYK-C 8001, a co-polymer with reactive groups, improves the mechanical strength and durability of fiber reinforced resins used in the blades. Based on our processing aids, our innovative Viscosity Control Technology (VCT) acts in the bonding pastes used to join components. Working in sync, Thixbreaker BYK-P 2710 and Thixbooster BYK-P 2720, help manufacturers to achieve the desired viscosity in each processing step.